Special Purpose Machinery
Custom De-palletising Tray Cutting Solution
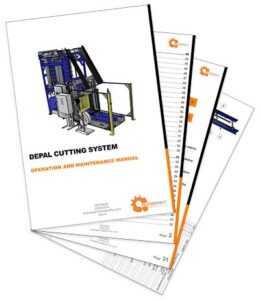
Comprehensive System Documentation
Our client searched for a solution that was readily available to suit their needs, however after extensive inquiries and they were unable to locate anything suitable. They turned to Automaint Solutions to design, manufacture and install a special-purpose custom-designed solution.
Our client’s requirements were for a fully automated custom machinery solution to receive pallet-sized, inverted tray, layer boards from an existing depalletising system. To then lower the trays to ground level and cut the corners, flatten the boards and neatly stack them. Once a desired height of boards is achieved, the stack is transported to a strapper before being transported to a pickup location for removal by forklift. This tidy and neatly strapped stack can then potentially be returned to a recycling plant.
There where many challenges with this project, lack of usable space, the inability to modify the automation system this special purpose machine attached too, and accomodating varying tray sizes. Automaint Solutions engineered a unique and elegant solution that delivered our client a solution that fulfilled all of their requirements.
Automaint Solutions managed this project from start to finish and were responsible for the CAD design, manufacture, electrical design and programming and finally installation, commissioning and training.
CAD Design
Manufacturing: Fabrication, Laser Cutting, Folding, Machining, Assembly
Electrical: Design, Installation, PLC & HMI Programming & SCADA Integration
Installation, Commissioning & Training
Documentation: User Manual, Electrical Drawings & Parts List
Robotic Case Packing System with Tecnobox Tray Erector
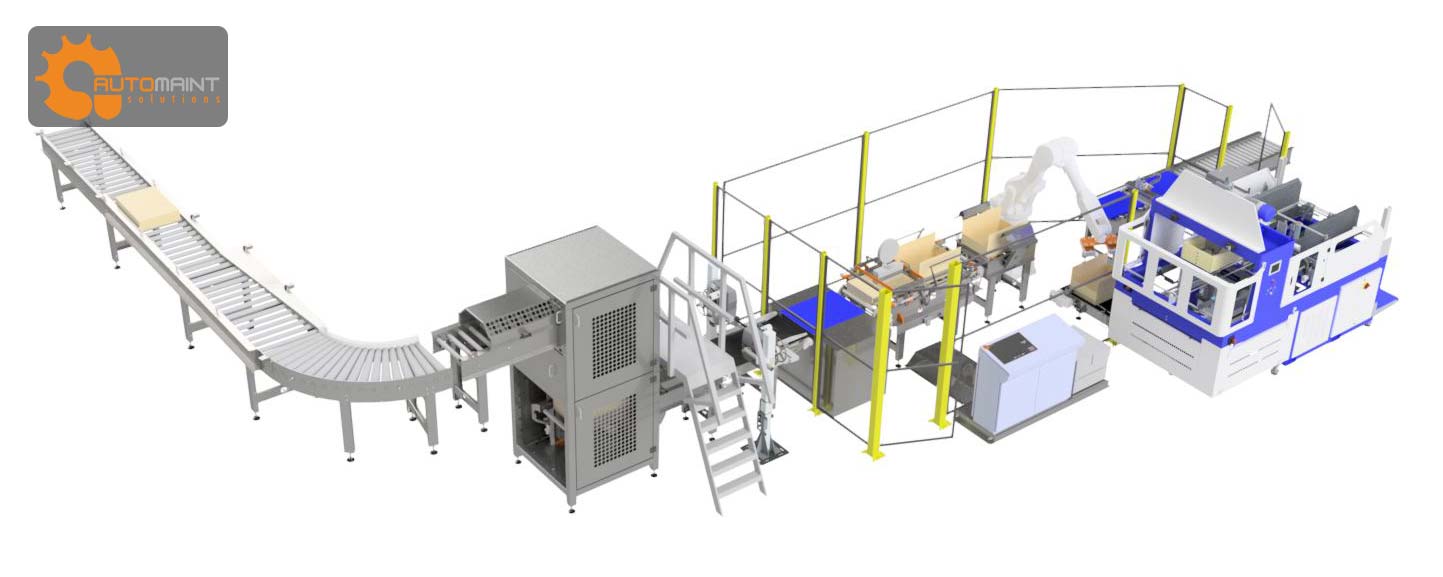
Our client was searching for a solution to automate the case packaging of their product into boxes produced by a tray erector and then transported from the case packaging system into their storeroom.
Automaint Solutions design engineers designed a solution in 3D CAD which used one of our Tecnobox TGOX2 tray erector machines, automated taping and labelling machines, a Kawasaki Robot and a range of a custom stainless steel conveyor systems using Interroll conveyor rollers to deliver the result the client demanded.
An additional challenge was, due to the layout of the client’s factory, a box elevator was required to get the finished boxes up to the height of the freezer storeroom.
Automaint Solutions designed the solution in 3D CAD software, manufactured the complete system, programmed the PLC & HMI user interface in our factory, before crating the entire system up and installing and commissioning the finished system in the customer’s facility.
We supplied a comprehensive user manual with the robotic case packing system. This included detailed electrical drawings, spare parts list for the entire system, along with a list of recommended spare parts for the client to keep in stock due to their isolated location.
Our client is now enjoying a fully automated robotic solution to get their products into cartons ready for dispatch to their customers worldwide and seeing significant financial benefits from the lower staff interaction with the packing process and lower work cover claims from the repetitive packing process.
Automaint Solutions managed this project from start to finish and were responsible for the CAD design, manufacture, electrical design and programming and finally installation, commissioning and training.
CAD Design
Manufacturing: Fabrication, Laser Cutting, Welding, Folding, Machining, Assembly
Electrical: Design, Installation and PLC/HMI Programming
Installation, Commissioning & Training
Documentation: User Manual, Electrical Drawings & Parts List
Custom Product Packaging Conveyor System
Due to production demands, our client required an additional food packaging conveyor line off their main production line.
Automaint Solutions was tasked with the complete 3D CAD design, manufacture, installation & commissioning of this project. Special attention to the existing infrastructure in place was required to ensure the new bolt-on system would not cause interference. This conveyor system includes sections to evenly space product on the conveyor belt and at the end of the conveyor line a product rotating section to rotate the product before it is passed to a flow wrapper.
We designed the complete system in 3D CAD, manufactured the more than 3,000 unique components that went into the final assembly, designed an electrical system and programmed both the HMI & PLC and performed the installation and commissioning.
We also supplied a comprehensive user manual, detailed spare parts documentation, recommended spare parts list and complete and detailed electrical drawings.
Automaint Solutions managed this comprehensive project from start to finish; CAD design, manufacture, machining, welding, parts procurement, powder coating, electrical design and assembly, on-site installation and commissioning.
Whether you need a simple conveyor solution, or a comprehensive integrated system like this one, Automaint Solutions will exceed your expectations for your special purpose projects.
CAD Design
Manufacturing: Laser Cutting & Folding, Welding, Machining & Assembly
Electrical: Design, Installation and PLC/HMI Programming
Installation & Commissioning
Documentation: User Manual, Electrical Drawings & Parts List
Screw Conveyor 500mm Diameter
Due to severe problems with an existing screw conveyor, which had required rewelding after several breaks in the auger and effectively reached the end of its useful life. Our client required an urgent screw conveyor manufactured to replace the existing unit.
Automaint Solutions completed a 3D CAD design which involved increasing the thicknesses and strength of various components to ensure a long life for the new screw conveyor. We then manufactured the new screw conveyor in less than 3 weeks and galvanised the trough and motor mount which will ensure a long-life in the meat processing facility this screw conveyor is installed in.
Automaint Solutions managed this special purpose project build from start to finish; 3D CAD design, manufacture, machining, welding, parts sourcing & galvanising.
Whether you need a simple screw conveyor solution or a comprehensively strengthed and re-engineered solution such as this screw conveyor, Automaint Solutions will exceed your expectations.
3D CAD Design
Manufacturing: Laser Cutting & Folding, Welding, Machining & Assembly
Grate Cover over Waste Water Pit
Automaint Solutions designed, manufactured & installed a replacement waste water pit cover, with new mechanical stirrer frames to replace a badly degraded & rusted cover for our customer. The whole frame was hot dip galvanised to ensure it will last as long as possible.
Carton Lifting Mechanism
No job is too small! Even a relatively minor change to a machine can result in benefits in productivity and cost savings. We CAD designed and manufactured a drop in replacement box lifting mechanism to a 40 year old carton erecting machine to eliminate operational issues our customer was experiencing with this machine. Problem solved!
Pallet Dispensing System
At the end of its service life with significant structural fatigue, Automaint Solutions was tasked with manufacturing and improving a pallet dispensing system. We re-designed parts of the original design to improve overall functionality and serviceability and ensuring that it could be installed without modifications to the control system.
Custom Bottle Washer Parts
Automaint Solutions was tasked by our customer to redesign the standard bottle rinser part to remove a design flaw that saw the parts breaking regularily. So we re-designed the part in 3D CAD, modelled, tested and finally manufactured new tougher parts for the bottle rinsing machine.
Filler CIP Cap
The customer was unable to purchase replacement parts for their bottle filling line, so they approached Automaint Solution to re-manufacture the parts so they could continue to use their filling lines. We CAD designed and manufactured the various components to ensure our customer was able to continue to clean their bottle filling line.
Bottling Line Transfer Conveyor Modification
Our customer was experiencing issues with the transfer of wine bottles from one conveyor to another conveyor line due to the poor design of the dead plate between the two lines. We were tasked with designing, manufacturing and installing a replacement conveyor to fix the problem.
Custom Guarding
Do you require updated guarding for older machines that no longer meet OH&S guidelines? Automaint Solutions can deliver a solution that typically involves 3D CAD designed and manufactured guarding. Our experienced technicians are able to fit and install the new guarding when it is convenient for you and the Automaint Electrical Department can update the electrical systems to ensure they meet Australian Safety Standards.
Enquiry Form
If you would like to discuss your Special Purpose Machinery problem with one of our engineering experts, please fill in your contact details in the form below and we will contact you as soon as possible.
Call Our Machinery Experts
If you’d like to speak to one of our engineering solutions experts please call us on
+61 3 9330 2678
Genuine 24/7 Service & Support
Our experienced and highly trained service technicians are only a phone call away, day or night, should you require advice, essential spare parts or a technicians on-site assistance with your machinery.
Learn More